しかしAGC株式会社 電子カンパニーの事業部長である木下健史(以下、木下)は「単なる増強ではない」と話す。その真意とは。EUVマスクブランクスの製造に携わる若手プロジェクト担当者の阪田一真(以下、阪田)と共に話を聞いた。
次世代半導体の製造過程で最も重要となる部材生産技術への挑戦
「EUVマスクブランクスの研究開発に着手したのは2003年。以前から開発していた半導体に回路パターンを焼き付ける露光機のレンズ材として使われる合成石英ガラスの高い技術と品質が、半導体製造技術を開発する米国のコンソーシアムSEMATECH(セマテック)から認められ、EUVマスクブランクス開発に向けたプロジェクトへの参画を要請されたことがきっかけでした。
EUVマスクブランクスとは、ゼロ熱膨張ガラス基板の表面に複数の組成からなる膜を積層したフォトマスクの原版で、EUV露光技術の中核をなす最も重要な部材です。AGCは、ガラス材料から研磨、成膜までの技術を垂直統合した世界で唯一のマスクブランクス・メーカーになることを目指しました」
そう話すのは、1989年に入社し、AGCの前身である旭硝子株式会社の時代からこれまで、エレクトロニクス分野での会社の成長に携わってきた一人でもある木下だ。
半導体において微細化が求められている今、その製造に用いられているのが極短波長のレーザー技術を搭載したEUV露光技術。この技術を実用化させるための重要部材である「EUVマスクブランクス」を、AGCは開発から15年もの年月を経て完成させた。
半導体の微細化とは、数mm角のチップ上に形成する電子回路素子や、それらをつなぐ配線のパターンの線幅を小さくすることを指す。線幅を小さくすることでより多くの回路を形成でき、その結果、処理速度の高速化や消費電力の減少などが可能となる。
次世代の半導体は我々の生活が便利になるだけでなく、グローバルな社会課題である消費電力削減に大きく貢献する存在でもあるのだ。
格段に高い要求に応えるため15年を要する
EUV露光技術ではフォトマスクと呼ばれる原版に描かれたパターンを、波長13.5nm(ナノメートル ※0.000000001m)の光を使ってウェハーに投影して転写する。その工程で使うフォトマスクの素材がマスクブランクスである。
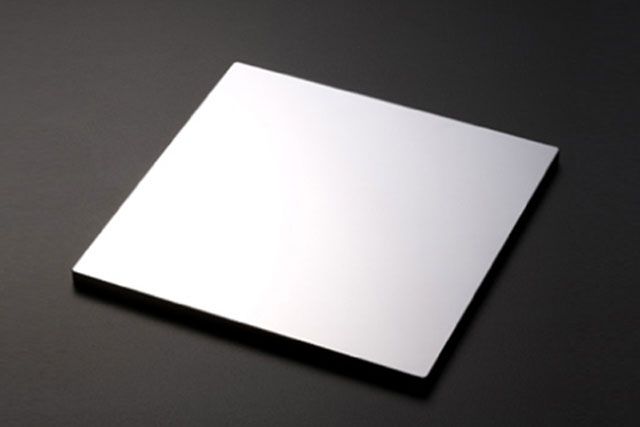
EUV露光用マスクブランクス
製造過程において、フォトマスクのゆがみやフォトマスクの表面に付着した微小なゴミ、表面の薄膜にできたわずかな欠陥が重大な加工不良を招く。
こうした問題を排除するため、基材になるガラスは熱膨張といった形状の変化を抑えるゼロ膨張ガラスにする必要がある。さらにガラス基板表面のゆがみを排除したうえで、波長13.5nmの光を反射する光学膜や吸収する光学膜を80〜100積層する。こうした積層膜は微小なゴミが混入することは許されない。
「EUVマスクブランクスで形成するパターンの線幅はわずか数nm。例えるなら直径約0.1mmの髪の毛の、10万分の1程度の幅です。
EUVマスクブランクスを野球のグラウンドと同じ程度の150m四方に拡大したとすると、その領域にスギ花粉(直径約30μm ※マイクロメートル 0.000001m)の半分程度のゴミが混入したら不良品になります」(阪田)
直径約15cmのものを150mに拡大したとしても、許されないゴミはμmレベル。そのため、従来品とは全く違う技術が必要とされた。木下はだからこそAGCの技術力で勝負できる分野になると考えたと話す。
「我々にとっては新規の分野でしたが、不利ではないと判断し技術開発をはじめました。80年代から培ってきた石英基板の技術やノウハウの進化、古くは建築用ガラスからディスプレイまで、社内で蓄積した薄膜形成技術を融合させることで製品化に辿り着きました」(木下)
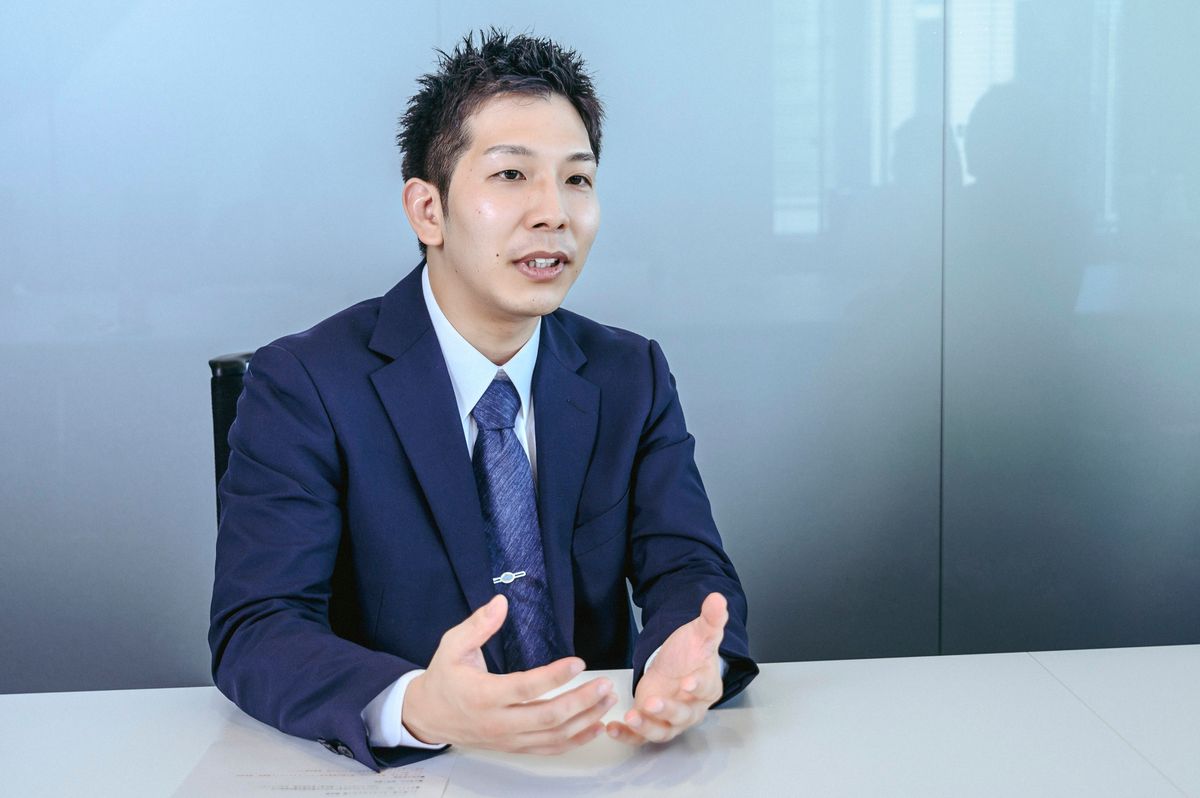
AGCエレクトロニクス株式会社 ブランクス部 検査技術グループ 阪田一真
また阪田は同社の強みを一気通貫にあると語る。
「EUVマスクブランクスを提供できる電子部材メーカーの数は世界でも現在2社のみ。AGCはその中でも世界で唯一、ガラス材料から研磨・洗浄・成膜までを1社ですべて手掛けることができ、AGCの幅広い技術領域を証明するような製品でもあります」(阪田)
AGCが手掛けるフォトマスクブランクスは顧客のニーズに対応できることが最大の強みである。高性能な半導体を製造するために欠かすことができない部材づくりへの挑戦は、まだ始まったばかりなのだ。
研磨技術でも微細化を実現
さらにもう一つ、半導体の微細化に貢献したAGCの素材が「セリアスラリー」だ。スラリーとは、半導体チップの表面の凹凸を、研磨粒子を使った物理的な加工と化学反応を組み合わせて高精度で研磨する液体状の研磨材のこと。
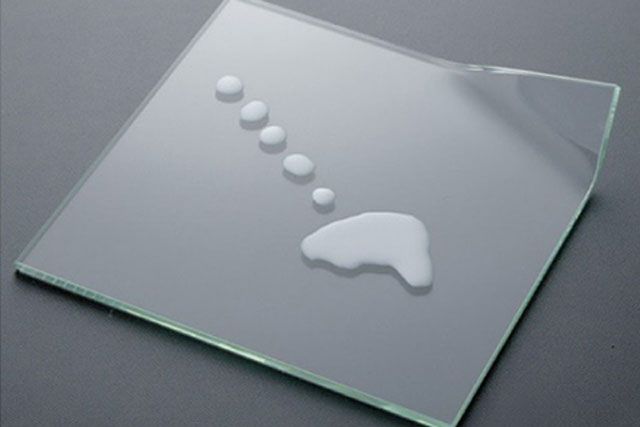
セリアスラリー
砥粒の材料が異なるいくつかのスラリーがある中で、微細化が進んで形状が複雑化した半導体表面の平坦化に向いているのがセリアスラリーだ。微細化が進むにつれて適用する工程を増やす半導体メーカーも多く、セリアスラリー需要の伸びにつながっているという。実はこのスラリーも、メインで扱っているのは世界で数社のみ。
「我々は有機材料も無機材料も持っている。様々なノウハウや知見を蓄積しているからこその強みだと思っています」(木下)
しかし高い技術を持ってしても、顧客の獲得には苦労したと話す。
「多くの半導体メーカーは使い慣れた部材を他メーカーの部材に切り替えることに慎重です。そこでAGCは顧客の製造条件に合わせたスラリーを提供できるように体制を整えました」(木下)
こうしたきめ細やかな対応も需要拡大へと繋がり、半導体分野でのシェアを広げていった。
2024年に約2倍の生産、2025年に400億円以上を目指す
半導体の微細化が進むことにより、より繊細かつ慎重な作業や適した材料が求められる中、最先端の技術を活かし、高い存在感を放つAGC。そこにこそ仕事の醍醐味があると阪田は語る。
「開発のスピードがとても速く、変化が激しいので楽しいことも辛いことも経験できる。常に前進している企業だからこそ刺激があり、日々学んでいけることがうれしいですね」(阪田)
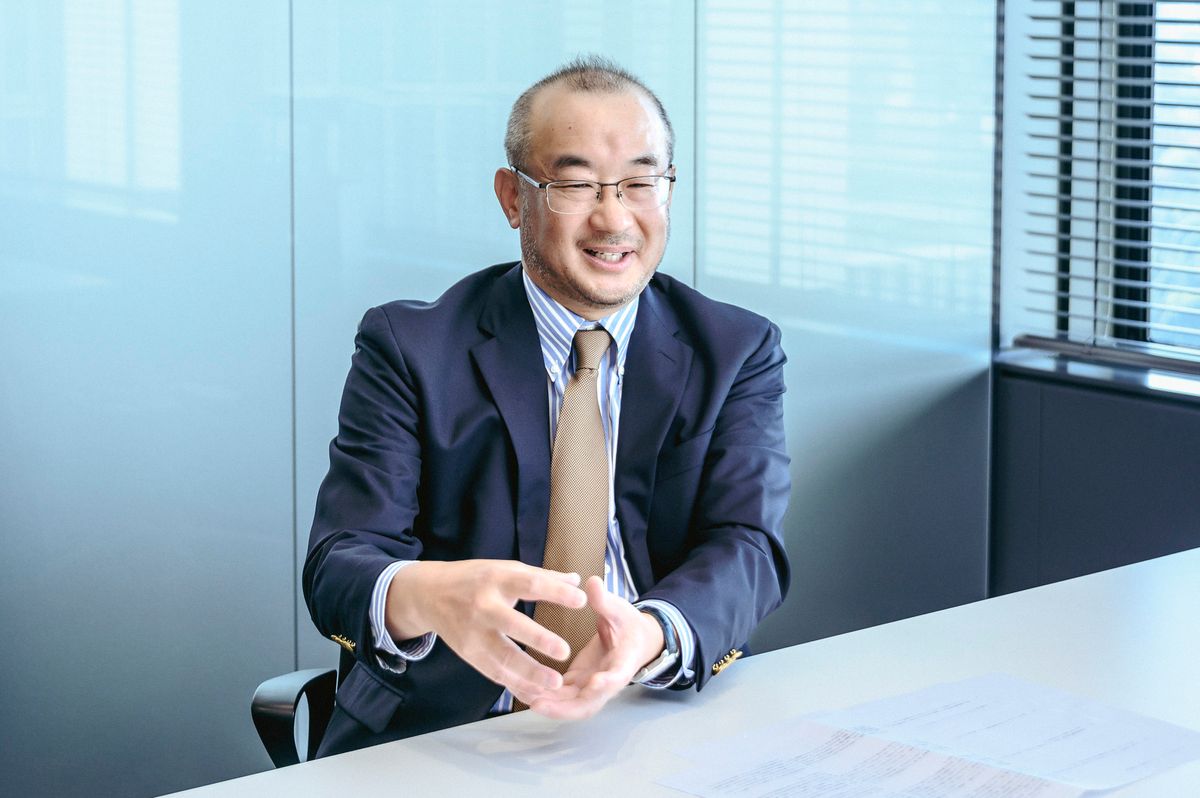
AGC株式会社 電子カンパニー 電子部材事業本部 アドバンストマテリアル事業部 事業部長 木下健史
一方の木下は、半導体の微細化がグローバルな社会課題への解決の一助となっていることに、やりがいを感じていると話す。
「半導体の微細化は古くから電子機器の処理速度の向上・小型化・省電力化で、快適な生活を実現してきました。半導体の集積度が2倍になると処理速度は2倍に、そして消費電力は1/4に削減されます。今後、半導体は個人だけでなく産業・国家の発展になくてはならない製品になっていきます。だからこそ、これからも自分自身を成長させ、半導体の進化に挑戦していきたいと思っています」(木下)
AGCはEUVマスクブランクスの生産能力を増強し、2025年までに売上高400億円以上を目指す。
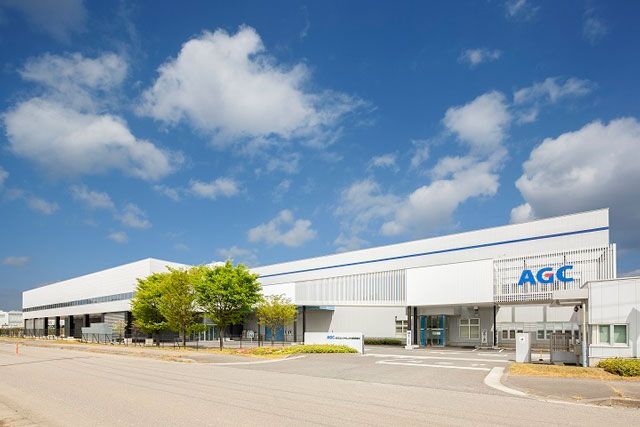
23年以降、段階的に生産能力の増強を行うAGCエレクトロニクス本宮事業所
AGCの前身となる旭硝子の創設者・岩崎俊彌が唱えた創業の精神『易きになじまず難きにつく』を実践するエレクトロニクス事業。半導体メーカーとして後発で参入し、15年の長期間にわたる開発で苦労したものの、今では半導体における微細化に大きく貢献する事業へと進化を遂げた。AGCの技術開発はこれからも世界をリードしていくに違いない。
AGC Hub|AGCのさまざまな挑戦はこちらから
https://www.agc.com/hub/index.html
木下健史(きのした・けんじ)◎1989年旭硝子(現AGC株式会社)に入社。エレクトロニクス部門に配属されたのち、製品知識を学ぶため工場の製造部門へ。2007年に半導体関連部材の製造を担当する。2018年からアドバンストマテリアル事業部長に就任。現在は電子カンパニー 電子部材事業本部 アドバンストマテリアル事業部 事業部長
阪田一真(さかた・かずま)◎2020年にエレクトロニクスの分野での開発職を希望し、AGC株式会社に入社。ブランクス部 検査技術グループ所属。入社より2021年までは最終研磨工程を担当。2021年より欠陥検査機を担当している