ロケットの金属部品には切削では作れない特殊な形状のものが多く、個別の部品をつなぎ合わせる必要がある。ロケットエンジンやタンクなどは、これまで過酷な条件に耐えられる特殊な金属を、高度な溶接技術でつなぎ合わせて作るのが普通だった。そのため、溶接技術がロケット開発においては非常に重要で、ロケット技術は溶接によって進歩し、同時に溶接はロケット技術によって進歩してきたという側面もある。しかし、パンチ工業は、溶接とは違うまったく新しい接合技術をロケット開発に持ち込もうとしている。
P-Basには、接合面を溶かす必要がなく、接合部分につぎ目がないために強度が高いというメリットがある。たとえば、内部に複雑な水管を通した金属部品の場合、通常は金属3Dプリンターで製作されるが、それでは使える材質が限られ、時間もかかる。P-Basなら汎用的な特殊鋼を幅広く使えるほか、加工時間は3Dプリンターの4分の1、接合部分の強度は素材本来の強度の90パーセント以上。さらに、接合前に水管内部をきれいに磨くことができるので仕上がりが違う。コスト、時間、品質の面で優れるということだ(トップの写真はP-Bas技術で製作した、複雑形状の水管を含有するダイカスト金型用コアピンとその内部構造)。
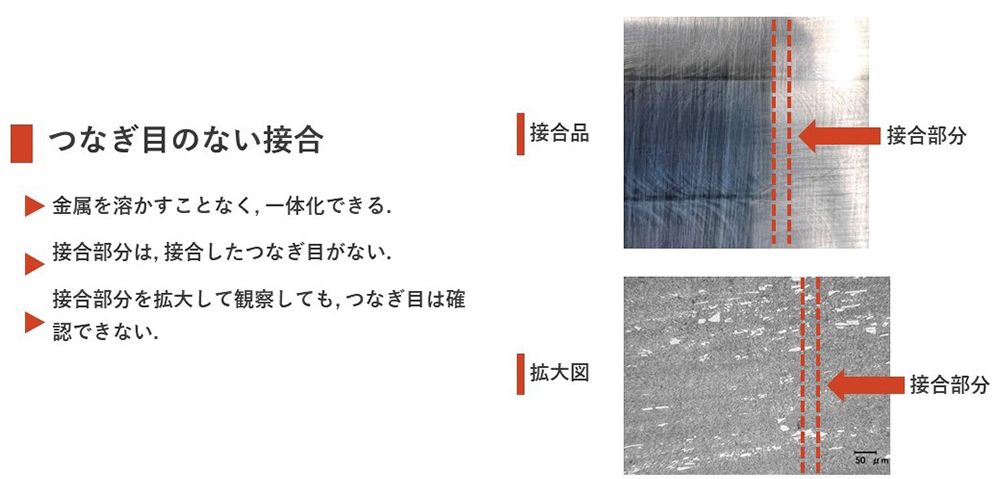
JAXAとの共同研究では、ロケットエンジンの耐熱合金材料に応用する場合の最適条件の確立と、圧力による歪みの改善を目指す。パンチ工業はすでに2016年から航空宇宙産業への参入を決めている。今年の5月には、月面探査車を開発する宇宙スタートアップ、ダイモンの技術パートナーとして、同社の月面探査車「YAOKI」の開発に加わることになった。この特殊技術で、日本の宇宙開発に活力を与えてほしいところだ。
プレスリリース