環境負荷を低減する製罐システム「aTULC(エータルク)」
どの実業分野でも、持続性の高い企業となっていくためには当然、製品やサービスの機能性、付加価値、そしてとくに今では環境対応を考えなければなりません。
実は今、プラスチックの代替として金属缶が注目されています。日本ではペットボトルのリサイクル率85%と比べて、スチール缶、アルミ缶のリサイクル率は90%以上。他の容器と比較して高い水準をキープしていて、循環型社会に貢献しているんです。
そんな金属缶の製法自体も時代の要請から変わってきています。弊社では「aTULC(エータルク)」という、環境負荷を低減した製缶システムを開発しました。
缶は、本来は金属板に「クーラント」という潤滑・冷却剤を塗って成形をして、大量の水で流して乾かして、内面には中身を保護するための塗料を塗ってオーブンで焼き付けて、と生産プロセスでの環境負荷が高かったのです。
一方「aTULC」では、缶の板の上に薄いプラスチックの膜をラミネートすることで、伸びがよい、油を塗らない「ドライ成形」が可能になりました。結果的に設備も省スペース化、簡略化が可能になったのです。
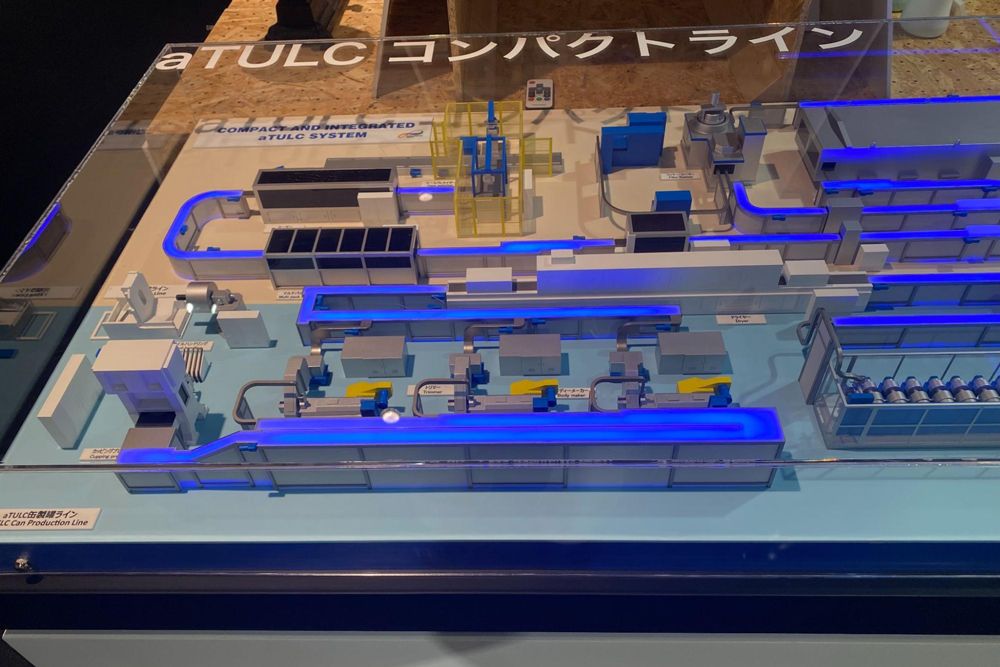
これまで製缶工場で製造された缶は、「空のまま」工場から飲料メーカーなどの工場に輸送され、そこで初めて中身を充填されて全国のお店に出荷されていました。本来、飲料メーカー側で充填と容器製造が一貫してできれば、輸送のコスト削減やトラックの排気ガスも削減できる。でも既存の製缶システムではそれが難しかったのです。それを「aTULC」が可能にした。
発想はペットボトルの製法システムでした。ペットボトルの場合は容器製造の投資額が低く、機械の運転や操作といったオペレーションが比較的容易で、導入設備も省スペースでまかなえるため、飲料メーカーが導入しやすいシステムでした。
加えて、とくに最近のペットボトルは本当に薄いので、中身を充填しないとつぶれる。つまり空ボトルのままではトラックに積めない。そんな素材的な事情もあって、もともと「中身を充填」してから輸送していたんですよね。そこで、製缶システムにペットボトルの良いところを取り入れ、飲料メーカーに導入しやすいシステムにできないか、と考えたわけです。
飲料メーカーの生産ラインに製罐プロセスを組み込むこのシステムは、「aTULCコンパクトライン」としてまるごと米国など海外にも輸出しています。
冒頭でお話ししたように、もともと戦前は1社で魚を獲る、缶を作る、缶に詰めるをやっていた、でもそれが輸出に適さなかったので「缶製造」だけをラインから切り離し、個別のプロセスにした。
その歴史を考えれば「aTULC」は逆に、1周回って元に戻ったといってもいいのですが、「システム、フルラインまるごとを海外輸出」することになったのは革新的な成果でした。缶を売ることが目的ではなく、環境負荷の低い製罐システムが全世界で広がることでよりサステナブルな容器の循環社会を作ることができる。創業者が食糧危機を解決しなければいけないと感じた時と同様に、こういった「使命感」こそが弊社の守るべきフィロソフィーだと考えています。
守るべきことを明確にし、高度な技術刷新を手段に、「かつてやっていたこと」へとより高度に、よりよく回帰する、イノベーションのひとつの形かもしれません。